
FREQUENTLY ASKED QUESTIONS
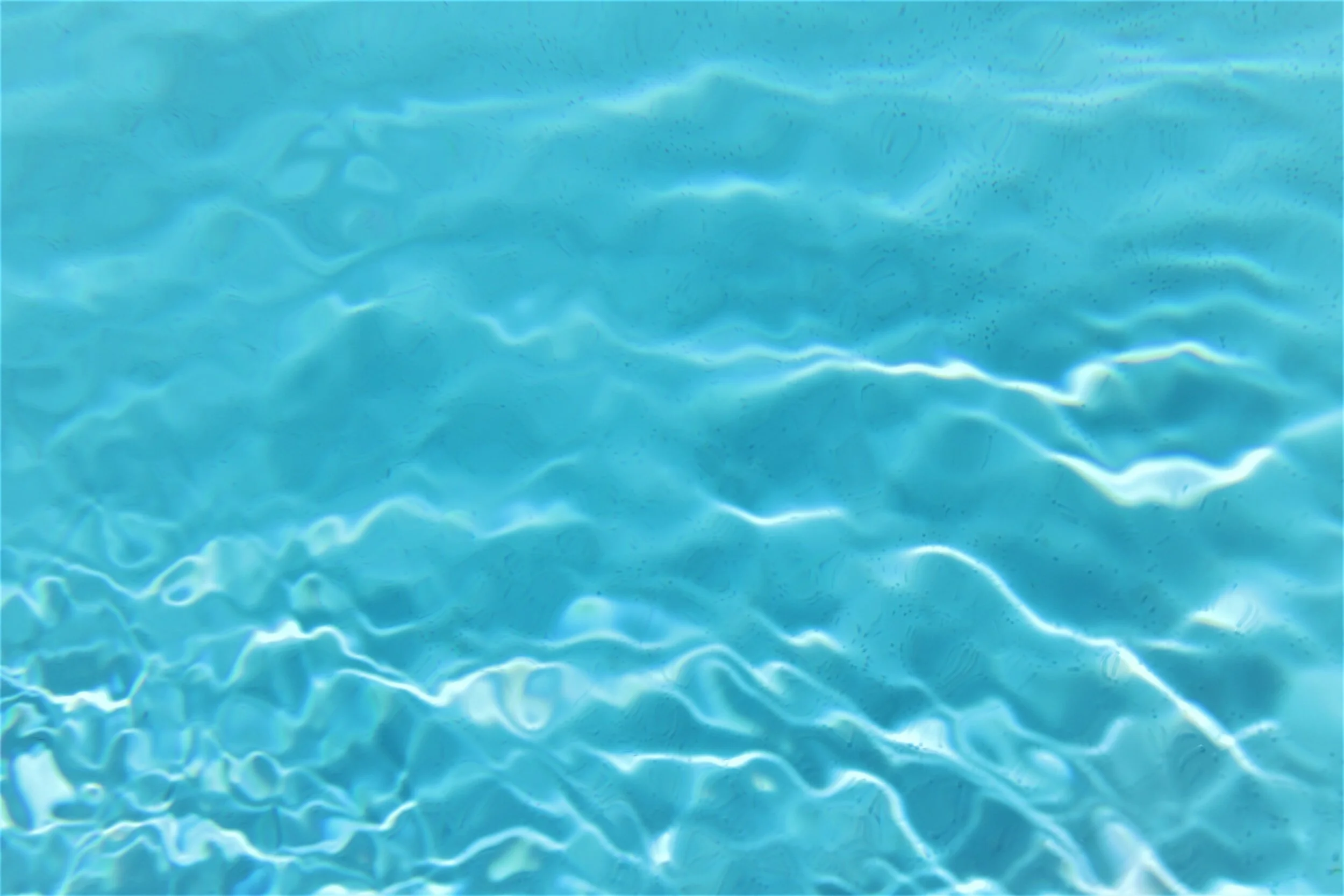
Peat Sorb is constantly working to solve difficult spill problems. We have developed natural products to meet the practical requirements of all stages of the clean up cycle while complying with applicable laws. Our absorbents are efficient, cost effective and minimize disposal costs. They are products that are totally compatible with today’s “green” outlook.
FAQs
-
Well actually, it can and it has. In May of 1994 a Brazilian land oil pipeline ruptured and dumped 2.7 million litres of oil into the environment. Within hours the oil had found its way into the Atlantic Ocean and soon contaminated an exotic local beach, threatening the natural ecosystem and destroying the local bathing and recreational facilities. The area was declared an environmental disaster of enormous proportions.
After valiant though futile attempts were made to clean up with mechanical means by local authorities, the area Peat Sorb distributor demonstrated the efficacy of the Peat Sorb product and soon tons of Peat Sorb was applied to the shoreline.
With two applications in just one day, the beach was virtually restored to its former state and after two weeks of sporadic applications to counter new contamination, the beach was opened, safely, to the public once again. Since then, Peat Sorb has performed oil spill clean-ups worldwide.
-
Peat Sorb is more cost effective overall, by using less product and providing for easier, greener disposal. Peat Sorb is environmentally safe in that it does not leach the hydrocarbon back into the soil or the groundwater. Peat Sorb makes water clean again. Unlike clay-based absorbents, Peat Sorb has no health risk warnings.
-
We have two solutions; Peat Sorb “Original” absorbs hydrocarbons and repels water and Peat Sorb “WHA” can solidify all the contaminated water along with binding all the hydrocarbons. We now offer two amazing Absorbents for your objectives.
On water, PEAT SORB can float for days attracting hydrocarbons through its wicking and capillary action drawing into its cellular structure the hydrocarbon, to replace where the cells were once full of water.
-
No. Once Peat Sorb has absorbed the hydrocarbon, it will not release it even under pressure. Peat Sorb has passed the Toxicity Characteristic Leachate Procedure (T.C.L.P. the Paint Filter and Liquid Release test.).
Peat Sorb will retain the hydrocarbon until the naturally occurring microbes found in the soil break down the hydrocarbon to its basic elements. We have also had the Peat Sorb tested at Michigan State University in a series of grass tests. When grass is exposed to an oil spill the grass will die if left untreated. Where the spill is treated with Peat Sorb the grass continues to grow even when the Peat Sorb is left in place, proving that the hydrocarbon does not leach out of the Peat Sorb.
-
Peat Sorb is an effective product in the suppression of volatile organic compounds (VOC’s). Peat Sorb has the ability to absorb flammable liquids and aid in the prevention of flashbacks. Peat Sorb will reduce the VOC’s from 100% to around 10%.
-
Please follow your local disposal requirements as they relate to the hydrocarbon. Peat Sorb can take a liquid hazardous hydrocarbon and solidify it to make it non-hazardous.
Save energy by using your used Peat Sorb as a source of fuel for burning! It will contribute about 15,000 – 15,500 BTU’s per pound and will assist in the incineration of absorbed oils. It is another way that Peat Sorb helps you contribute to an efficient, green and environmentally responsible way of running your business. If ignited accidentally, Peat Sorb burns with a controlled wick action and helps reduce the potential for explosive combustion. Peat Sorb does not leach the hydrocarbon back into the environment, so it can safely be buried in landfills according to your local regulations. Soil and groundwater will not be contaminated by the hydrocarbon.
-
Acetone
Acetronitrile
Amvl Acetate
Battery Acid
Benzene
Blood
Butanol
2-Butanone
Bromodichloromethane
Bromoform
Carbon Disulfide
Carbon Tetrachloride
Chloroform
Chloromethane
Chlorobenzene
Crude Oil
Cutting Oils
Cvclohexane
Dichlorobenzene
1, 2-Dichloroethene
Diesel Fuels
Ethanol
Ethylbenzene
Ethyl Ether
Ethylene Glycol
Gasoline
Glycerine
Heptane
Hexane
Hexachlorobenzene
Hexachlorobutadiene
Hexachloroethane
Hydrochloric Acid
Hydrofloric Acid
Isobutanol
Isopropene
Isopropanol
Jet Fuels
Kerosene
Methanol
Methylene Chloride
Methyl Ethyl Ketone
Methylphenol
Motor Oils
Muriatic Acid
Napthanlene
2-Nitroaniline
Nitrobenzene
PCB’s
Perfluorooctanesulfonic
Acid (PFO)
Pentane
Pentachlorphenol
Phenol
Propanol
Styrene
Sulphuric Acid
Teytrachloroethane
Tetrachloroethylene
Tetrahydrofuran
Toluene
Trichloroethylene
Trichlorophenol
Trichlorophenoxyacetic
Acid (Ingredient in Agent
Orange)
Varsol
Vinyl Acetate
Vinyl Chloride/ Xylenes
And many more!
-
Airports
Armed Services
Auto Wreckers
Beach Cleanup Crews
Boaters
Camp Grounds
Car Manufacturers
Chemical Companies
Car Shows
Construction Sites
Cruise Ships
Dealerships
Elevator Companies
Factories
Farms (Agricultural,
Animal and Fish)
Fire Departments
Food Industry
Gas Stations
Golf Courses
Government
Haz Mat Teams
Hospitals
Hotels
Hydro
Machine Shops
Marinas
Military
Mines
Morgues
Navy
Oil Refineries
Paint Manufacturers
Parking Lots
Petroleum Industry
Ports and Harbours
Power Plants
Race Tracks
Railroads
Recreational Vehicles
Retail Outlets
Service Garages
Shipyards
Spill Contractors
Steel Companies
Subways
Tool & Dye Makers
Transit Authorities
Transportation Trucks
Waste Haulers
Wind Turbine Facilities
-
Options for Drilling Contractors to dispose of drill spoils are becoming increasingly limited. One alternative is to have a liquid waste disposal company haul the material off, which can be expensive. Another alternative is to try and settle out the material in tanks, which can be minimally effective and time consuming. Centrifuge dewatering equipment is expensive and cost can only be justified on very large projects.
Wood chips, for example, are frequently used as a solidification agent, but because wood chips are minimally effective as an absorbent, using wood chips as a solidification agent can double the volume of material to be disposed of.
The initial price of some solidification agents, such as wood chips, fly ash, cement kiln, dust and sawdust may appear cheap. However, the overall operational cost can be astronomical when you consider costs of trucking the material to the project, trucking the large volume of solidified material away and increased landfill tipping fees.
Peat Sorb or WHA if high water ratio, can be poured into or across the surface of a waste slurry pit and stirred into the slurry with a backhoe or excavator.
Solidification can be a viable and cost-effective method of dealing with liquid or semi-solid material and Peat Sorb’s technologies are available to ease the burden of drill spoils disposal.
The simple process of solidifying drill spoils involves taking liquid or semi-solid slurry and then bonding it together with Peat Sorb so that the end product becomes a solid (no free liquids).
The processed material now encapsulated in Peat Sorb or WHA can be discharged directly into roll-off boxes or dump trucks, or simply discharged into a burmed area where it can be stockpiled before loading for haul-off or mixed with native soil for onsite disposal. Although the processed material no longer contains free liquids, the material will continually reduce in moisture content and shrink in volume when allowed to set exposed to the sun and wind.
As regulations and restrictions on drill spoils’ disposal tighten, Contractors must become better educated on these regulations and restrictions, as well as the disposal alternatives available.
Peat Sorb as an organic proven solidifier is cost effective as it outperforms with less product, so less to dispose of.
Lab tested safe for landfill. Peat Sorb is always the Best Solution
More than 90% of oil slicks are caused by shipping and human activity on land. How can Peat Sorb help?
Data Source Link Click Here